So finden Sie die richtige Instandhaltungsstrategie für Ihr Industrieunternehmen
Die Industrie 4.0 – wie der Einsatz von intelligenten und digital vernetzten Systemen in Industrieanlagen gerne plakativ bezeichnet wird – hat auch im Industrieservice einen Wandel eingeläutet. Immer mehr Unternehmen orientieren sich um: Sie nutzen neue Strategien in der Instandhaltung. Wir stellen die wichtigsten Instandhaltungsstrategien vor.
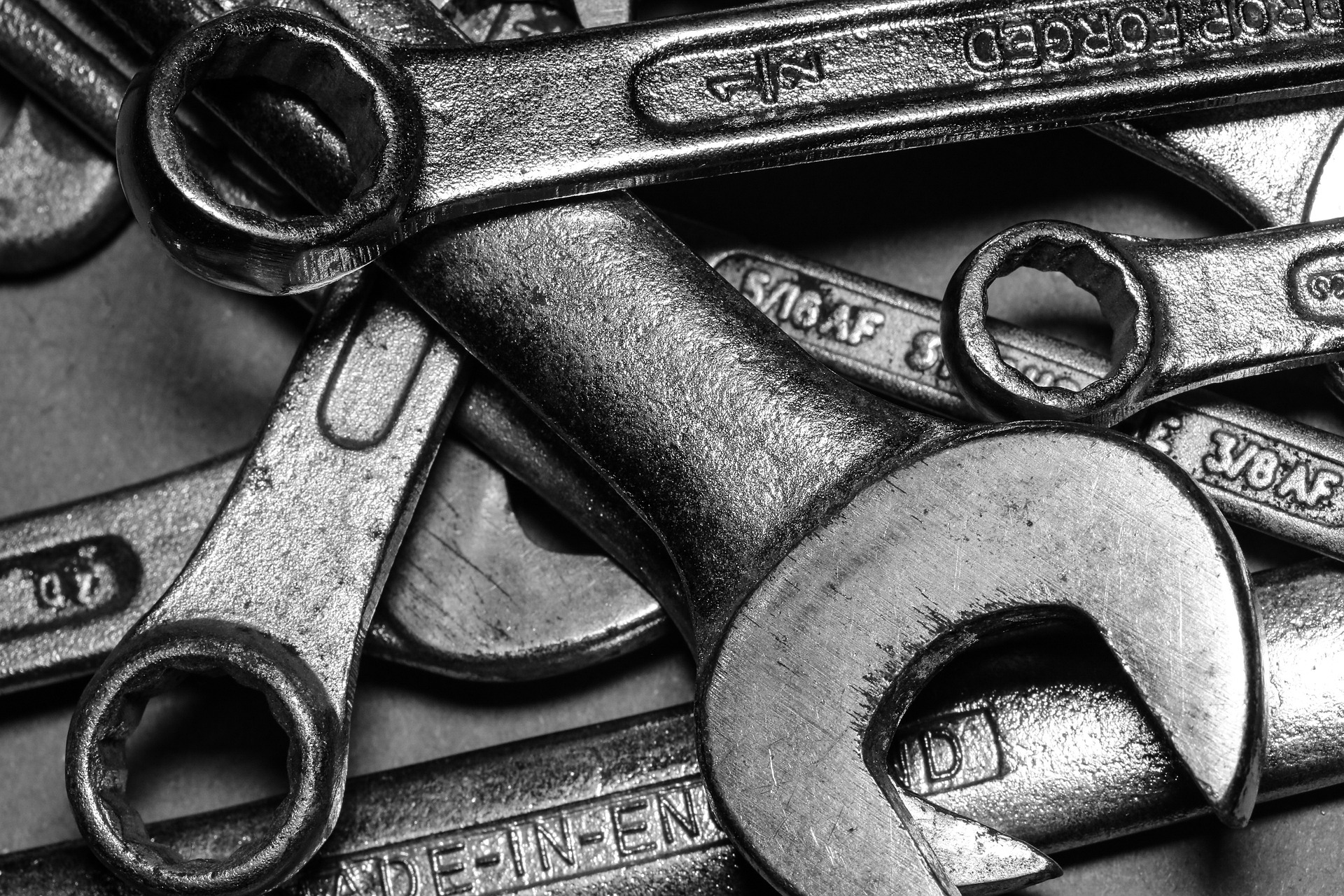
Die moderne Informationstechnik hat in den vergangenen Jahren mit großen Schritten Einzug in deutsche Produktionsanlagen gehalten. Die Industrie 4.0 – wie der Einsatz von intelligenten und digital vernetzten Systemen in Industrieanlagen gerne plakativ bezeichnet wird – hat auch im Industrieservice einen Wandel eingeläutet. Immer mehr Unternehmen orientieren sich um: Sie nutzen neue Strategien in der Instandhaltung. Statt auf die klassische reaktive Instandhaltung setzen sie auf präventive Instandhaltung, zustandsorientierte Instandhaltung oder vorausschauende Instandhaltung, um Ausfallzeiten zu minimieren und Kosten zu sparen.
In diesem Blogartikel erläutern die Experten der GP Prüfservice die Vorteile der unterschiedlichen Instandhaltungsstrategien und das Zusammenspiel mit Elektroprüfungen wie der DGUV V3 Prüfung.
Moderne Instandhaltungsstrategien und Elektroprüfungen sind zwei Komponenten, die nahtlos zusammenarbeiten, um die Betriebssicherheit und Effizienz in Ihrem Unternehmen zu gewährleisten. Aber wie genau ergänzen sich diese beiden Elemente und schaffen einen Mehrwert für Ihre Betriebsabläufe?
Instandhaltungsstrategien dienen dazu, die Effizienz und Lebensdauer Ihrer Maschinen und elektrischen Geräte zu maximieren. Dabei geht es darum, durch proaktive Maßnahmen potenzielle Störungen und Ausfälle frühzeitig zu erkennen, bevor sie sich auf die Produktivität auswirken. Dies wird durch regelmäßige Überprüfungen, Wartung und vorbeugende Maßnahmen erreicht.
Auf der anderen Seite stehen Elektroprüfungen, die eine entscheidende Rolle bei der Gewährleistung der elektrischen Sicherheit spielen. Sie dienen dazu, die Einhaltung der gesetzlichen Vorschriften sicherzustellen, die von der DGUV V3 geregelt sind. Außerdem tragen sie dazu bei, die Sicherheit Ihrer Mitarbeiter zu gewährleisten.
Wenn wir nun diese beiden Komponenten miteinander kombinieren, entsteht eine Synergie, die weit über die einzelnen Vorteile hinausgeht. Mit einer optimal abgestimmten Instandhaltungsstrategie können Elektroprüfungen effektiv in den laufenden Betriebsablauf integriert werden, wodurch Störungen minimiert werden und die betriebliche Effizienz verbessert wird. Potenzielle Risiken und Ausfallzeiten werden effektiv reduziert.
Sie fragen sich, welche Instandhaltungsstrategie für Ihr Industrieunternehmen die richtige ist? Dann finden Sie in diesem Blogbeitrag viele hilfreiche Informationen. Die Experten der GP Prüfservice GmbH erläutern die Vor- und Nachteile der unterschiedlichen Ansätze. Wir blicken zurück auf jahrzehntelange Erfahrung im Industrieservice und beraten Sie gerne auch dazu, wie Sie unsere Elektroprüfung effizient in die aktuelle oder künftige Instandhaltungsstrategie Ihres Unternehmens integrieren. Rufen Sie uns an!
Jetzt individuell beraten lassen
Clevere Instandhaltung senkt die Kosten in der Industrie
Früher war es üblich, eine Industrieanlage erst dann zu reparieren, wenn Sie kaputt ist. Inzwischen gehen viele Unternehmen dazu über, ihre Maschinen regelmäßig und vorbeugend einer Wartung zu unterziehen. Immer häufiger fällt auch die Bezeichnung Predictive Maintenance - ein Begriff, der einen Paradigmenwechsel in der Industrie 4.0 mit sich bringt. Es geht nicht länger darum, Defekte im Zuge einer Wartung zu erkennen und darauf zu reagieren, sondern eventuelle Probleme im Vorfeld zu ermitteln. Das Monitoring, die permanente Überwachung von Maschinen durch Messtechnik also, ist deshalb ein Grundpfeiler moderner Instandhaltung.
Zustandsorientiert, vorausschauend, vorbeugend - für den Laien wird es bei diesen Bezeichnungen schnell verwirrend. Werfen wir deshalb nun einen Blick auf die Unterschiede der modernen Instandhaltungsstrategien.
Vorab sei betont: Es gibt keine allgemein gültige Regel, welche Strategie zur Instandhaltung für welches Unternehmen passt. Die richtige Instandhaltungsstrategie ist immer abhängig von den individuellen Gegebenheiten. Häufig ist eine Kombination mehrerer Strategien zielführend. Als Unternehmer oder Betriebsleiter sollten Sie deshalb Ihre Bedürfnisse genau analysieren und anschließend wählen, welche Instandhaltungsstrategien am besten zu Ihren Anlagen passt.
Wie bereits erwähnt, unterteilen sich die möglichen Instandhaltungsstrategien in die reaktive, die vorbeugende (= präventive), die zustandsorientierte und die vorausschauende Instandhaltung (= Predictive Maintenance). Bevor wir in den folgenden Kapiteln ausführlich auf die vier Ansätze eingehen, hier die Kernpunkte auf einen Blick
Als Unternehmer können Sie sich für eine der vier Strategien entscheiden oder eine Kombination wählen, die auf Ihre Anlagen, deren Alter und die einzelnen Anlagenkomponenten abgestimmt ist. Die Orientierung an den gesetzlichen Rahmenbedingungen und den Empfehlungen des Herstellers spielen in allen Instandhaltungsstrategien eine maßgebliche Rolle und sind somit auch im Zeitalter der Industrie 4.0 von Bedeutung.
Bei der reaktiven Instandhaltung handelt es sich um eine Strategie, die in der Vergangenheit Gang und Gäbe war. Es wurde nur repariert, wenn sich im Zuge einer Wartung oder einer Elektroprüfung Defekte und Verschleiß zeigten oder wenn Maschinen und Anlagen aufgrund von Defekten ausfielen. In vielen Unternehmen wird diese Instandhaltungsmethode auch heute noch angewandt, obwohl die reaktive Instandhaltung nachweislich mit Mehrkosten und einem höheren finanziellen Aufwand für die Instandsetzung einhergeht.
Wird ein Defekt erkannt oder weist ein Betriebsmittel Anzeichen von Verschleiß auf, reagiert der Unternehmer und lässt das betroffene Teil austauschen. Diese Methode führt leider sehr häufig dazu, dass Anlagen plötzlich und über einen längeren Zeitraum ausfallen – zum Beispiel, weil ein Ersatzteil fehlt. Dies stellt Industriebetriebe damit vor das Problem, dass sie ihre Ressourcen nicht vollständig nutzen können und mit finanziellen Einbußen rechnen müssen. In der Industrie 4.0 verliert der reaktionäre Aspekt in den Instandhaltungsstrategien immer mehr an Bedeutung. Wenn ein Defekt auftritt, wird natürlich nach wie vor repariert. Das Ziel ist aber, dass es gar nicht erst soweit kommt.
Präventivmaßnahmen in der Instandhaltung basieren auf im Vorfeld festgelegten Zeitintervallen, die sich in der Regel an den Laufzeiten der Maschinen und Anlagen orientieren. Zur Durchführung präventiver Instandhaltungsmaßnahmen werden die Anlagen regelmäßig heruntergefahren und auf Verschleiß, defekte Bauteile oder Materialschwächen und Funktionseinschränkungen hin kontrolliert. Die präventive Instandhaltung hat zwar den Vorteil, dass manchem Defekt vorgebeugt werden kann. Aber es kommt nicht selten vor, dass noch funktionsfähige Bauteile ausgetauscht und vorhandene Restlaufzeiten nicht vollständig genutzt werden. Als Unternehmer müssen Sie daher mit enormen Mehrkosten rechnen. Sie geben Geld aus für unnötige Instandsetzungsmaßnahmen.
Die präventive Kontrolle steigert also die Lebensdauer und Verfügbarkeit industrieller Anlagen, doch der Preis ist in diesem Fall sehr hoch. In Kombination mit anderen Maßnahmen kann die präventive Instandhaltung durchaus ein geeignetes Mittel sein. Für sich betrachtet ist die vorbeugende Instandhaltung aber inzwischen nicht mehr zeitgemäß.
Die zustandsorientierte Instandhaltung ist eine zeitgemäße Strategie, durch die Sie Ihre Ressourcen sehr gut ausnutzen und gleichzeitig Kosten einsparen. In den verfügbaren Instandhaltungsstrategien gewinnen zustandsorientierte Maßnahmen immer mehr an Bedeutung und sind ein wichtiger Bestandteil der Industrie 4.0. Ziel der zustandsorientierten Instandhaltung ist es, für notwendig befundene Instandhaltungsmaßnahmen zeitlich, qualitativ und kostenoptimal zu kalkulieren und zu realisieren.
Aber wie funktioniert zustandsorientierte Instandhaltung? Mit modernster Messtechnik ist es heute problemlos möglich, den Ist-Zustand Ihrer Anlagen und Maschinen präzise zu erfassen und zu bewerten. Das Monitoring nimmt hier einen äußerst wichtigen Stellenwert ein. Denn nur, wenn Sie exakt über den Zustand aller Komponenten informiert sind, können Sie für maximale Effizienz sorgen und sich gleichzeitig vor Ausfällen schützen. Der Vorteil im Vergleich zur vorbeugenden Instandhaltung: Ein Betriebsmittel wird erst dann ausgetauscht, wenn es wirklich abgenutzt ist – und nicht, wenn ein Wartungsplan dies vorsieht.
Anders herum gilt dies genauso: Zeigt ein Bauteil stärkere Abnutzungserscheinungen als erwartet, wird es rechtzeitig gewechselt – und nicht erst, wenn es turnusgemäß an der Reihe ist. Dank der beschriebenen und bewerteten Messergebnisse erkennen Sie Ursachen für eine mögliche Störung oder einen bevorstehenden Anlagenschaden im Vorfeld und haben die Möglichkeit, vorausschauend zu agieren und die Beseitigung in Zukunft erwarteter Defekte in die Wege zu leiten. Dabei wird der Abnutzungsvorrat in vollem Umfang genutzt und Sie schließen Primärschäden aus, wodurch es generell nicht zu kostspieligen Folgeschäden und den damit verbundenen Ausfällen kommt.
Es gibt verschiedene analytische Verfahren, beispielsweise die Schwingungsanalyse, durch die in Kürze auftretende Schäden frühzeitig erkannt und entsprechend behandelt werden können. Condition Monitoring wird zur Überwachung des Zustandes eingesetzt und dient der Erfassung sowie der Bewertung des aktuellen Anlagen- und Maschinenzustandes. Für die zustandsorientierte Instandhaltung muss der laufende Betrieb nicht unterbrochen werden, da das Monitoring im rotierenden Zustand möglich - sensibler Messtechnik sei Dank. Die stetige Zustandsüberwachung bietet enorme Vorteile in den Bereichen Sicherheit, Verfügbarkeit und Effizienz aller technischen Anlagen und industriellen Maschinen.
In der Predictive Maintenance, der vorausschauenden Instandhaltung, werden wie bei der zustandsorientierten Instandhaltung permanent alle Bauteile einer Industrieanlage durch sensible Messtechnik überwacht. Die vorausschauende Instandhaltung geht aber noch einen Schritt weiter. Durch intelligente Analyse der unterschiedlichsten Daten wird es quasi möglich, einen Blick in die Zukunft zu werfen. Die Instandhaltung wird daran ausgerichtet, was höchstwahrscheinlich passieren wird.
Die ermittelten Daten setzen sich aus verschiedenen Parametern zusammen und stammen aus unterschiedlichen Quellen. Beispielsweise werden zusätzlich zu den Messwerten auch die Herstellerdaten berücksichtigt. Data Mining und die permanente Analyse machen es möglich, selbst sehr komplexe Zusammenhänge zu erkennen. Das System liefert präzise Ergebnisse für die Ausfallwahrscheinlichkeit und gibt eine Prognose darüber ab, welche Instandhaltungsmaßnahmen notwendig sind.
Der große Vorteil von vorausschauender Instandhaltung: Wenn Sie in Ihrem Unternehmen auf Predictive Maintenance setzen, gehören ungeplante Ereignisse der Vergangenheit an. Sie können Ihr Budget für die Wartung Ihrer Maschinen und Anlagen verlässlich kalkulieren und dennoch flexibel reagieren. Zum Beispiel, indem Sie stark ausfallgefährdete Komponenten instandsetzen, während Sie weniger wichtige Wartungsmaßnahmen vorübergehend aussetzen können.
Was ist nötig für den Einsatz von Predictive Maintenance?
Das Konzept der Predictive Maintenance basiert auf der Ausstattung von Maschinen und Anlagen mit moderner Sensorik. Ultraschall nimmt in den Technologien intelligenter Instandhaltungsstrategien eine führende Position ein. Mit Ultraschall ist es möglich, drohende Ausfälle rechtzeitig zu erkennen und die Wahrscheinlichkeit eines Defekts in absehbarer Zeit vorauszusagen.
Gute Argumente für vorbeugende Instandhaltung
Dass die reaktive Instandhaltung als Auslaufmodell gilt, ist längst bekannt. Aber auch die vorbeugende Instandhaltung hat in immer mehr Industriebetrieben ausgedient, da Sie häufig den sinnlosen Austausch funktionierender Bauteile mit sich bringt und dadurch hohe Kosten verursacht. Nur mit zustandsorientierten oder vorausschauenden Instandhaltungsmaßnahmen können Unternehmen ihre vorhandenen Ressourcen optimal nutzen und ihr Potenzial ausschöpfen.
Sparen mit zustandsorientierter Instandhaltung
Mit zustandsorientierten Instandhaltungsmaßnahmen können Sie Ihre Kosten durchschnittlich um 15 bis 23 Prozent senken. Sie senken zudem die Produktionsausfallrate um 16 bis 36 Prozent und die Stillstandszeiten um 20 bis 35 Prozent.
Zusammenfassung: Instandhaltungsstrategien der Zukunft – darauf kommt es an
Moderne Instandhaltungsstrategien ermöglichen es Industrieunternehmen, Probleme an Produktionsanlagen frühzeitig zu erkennen und gleichzeitig die Instandhaltungskosten zu reduzieren. Statt nur bei Defekten zu reparieren (hohes Ausfallrisiko) oder vorbeugende Wartung zu betreiben (hohe Kosten), überwachen sie Ihre Anlagen mit sensibler Messtechnik und führen Instandhaltungsmaßnahmen zum idealen Zeitpunkt durch.
Eine Kombination verschiedener Instandhaltungsstrategien ist dennoch zielführend, da die Auswahl der richtigen Strategie immer auf die einzelnen Komponenten der Anlagen und Maschinen abgestimmt werden sollte. Vorausschauende Instandhaltungsstrategien sind prinzipiell für große, mittelständische und kleine Industrieunternehmen zielführend. Aber nicht jede Strategie eignet sich für jedes Unternehmen.
Wie wird Instandhaltung definiert?
Der Instandhaltungsbegriff wird in den DIN-Normen DIN 31051 und DIN EN 13306 definiert und strukturiert. Der Begriff umfasst alle Maßnahmen, die dafür sorgen, dass eine so genannte Betrachtungseinheit funktionsfähig bleibt oder wieder wird. Instandhaltungsmaßnahmen sind Wartung, Inspektion, Instandsetzung und Verbesserung.
Was ist eine Betrachtungseinheit
Bei der Betrachtungseinheit handelt es sich um einen sehr allgemeinen und variablen Begriff für das Betriebsmittel oder die Anlage, die gewartet oder repariert werden soll.
Was ist der Unterschied zwischen zustandsabhängiger und vorausschauender Instandhaltung?
Bei zustandsabhängigen Instandhaltungstätigkeiten wird durch eine permanente Zustandsanalyse mit moderner Messtechnik sichergestellt, dass der Abnutzungsvorrat des Bauteils optimal ausgenutzt wird. Predictive Maintenance geht noch weiter und errechnet anhand von Erfahrungswerten und Wahrscheinlichkeiten schon im Vorfeld, wann eine Instandhaltungsmaßnahme fällig ist. Neben der Zustandsanalyse wird also noch ein Blick in die Zukunft gewagt. Wenn man Stillstandszeiten im Voraus planen und minimieren kann, trägt dies zu geringeren Instandhaltungskosten bei.
Was ist ein Abnutzungsvorrat?
Ein Verschleißteil geht bei permanenter Zustandsanalyse in der Regel nicht von heute auf morgen kaputt, sondern verschleißt langsam. Der Abnutzungsvorrat ist in diesem Zusammenhang der Spielraum den ein Bauteil oder Betriebsmittel hat, ehe es eine Störung verursacht. Die Instandhaltungstätigkeiten sollten idealerweise erst dann erfolgen, wenn der Abnutzungsvorrat fast ganz aufgebraucht ist - aber eben auch nicht zu spät, um Primärschäden und Folgeschäden zu vermeiden.
Sie können sich in allen Bereichen der DGUV V3-Prüfungen auf uns verlassen.
Die GP Prüfservice GmbH ist Ihr Partner für DGUV V3 Prüfungen bundesweit. Ob Sie Ihre ortsfesten Maschinen, ortsfesten Anlagen oder ortsveränderlichen Geräte prüfen lassen möchten, eine Gefährdungsbeurteilung oder eine VdS-Sachverständigenprüfung benötigen – GP Prüfservice ist Ihr Ansprechpartner. Auch beim Thema E-Mobilität sind wir für Sie da und prüfen Ladesäulen, Ladekabel oder Wallboxen.
Prüfung elektrischer Anlagen
Prüfung elektrischer Betriebsmittel
Prüfung elektrischer Maschinen
VdS-Sachverständigen-Prüfung
E-Mobilität
Gefährdungsbeurteilung
Ein reibungsloses Prüfprojekt beginnt mit einer sorgfältigen Vorbereitung
Machen Sie jetzt den ersten Schritt zu einem reibungslosen Prüfprojekt mit den Prüfkonzepten von GP Prüfservice.
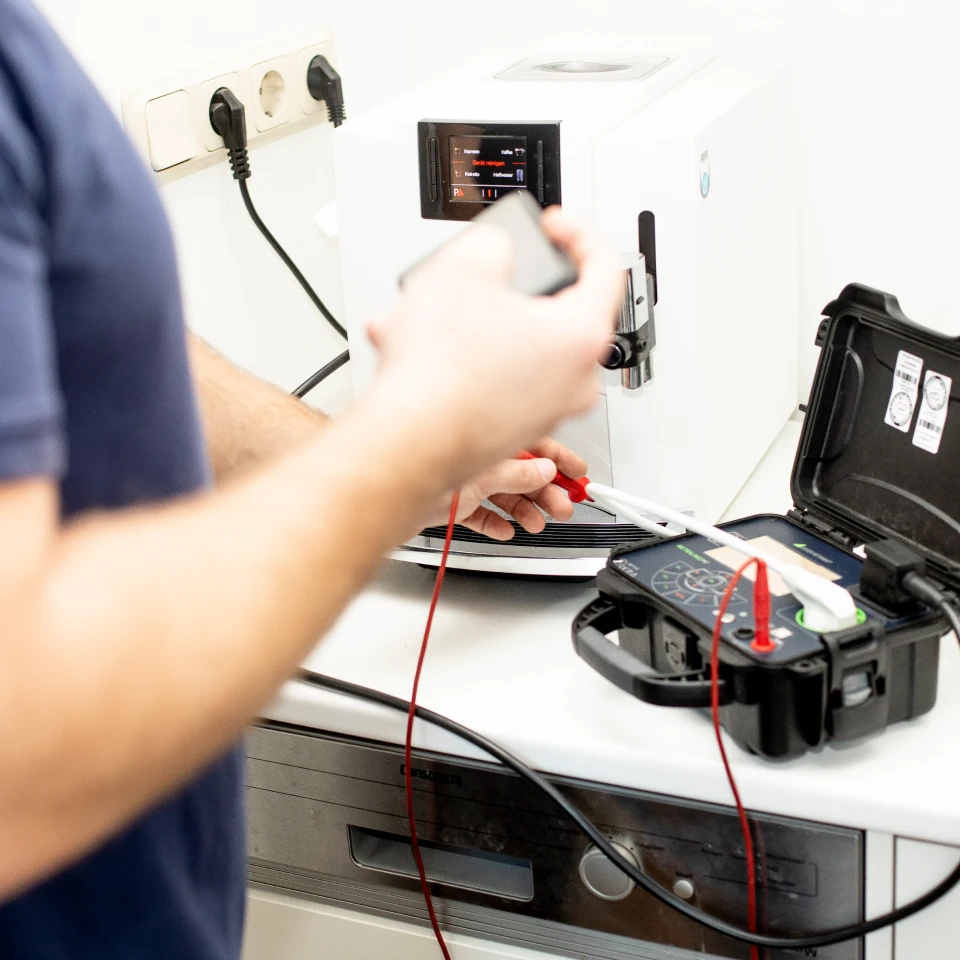